Discover What is Porosity in Welding and Its Result on Structural Integrity
Wiki Article
Recognizing Porosity in Welding: Exploring Causes, Results, and Prevention Methods
As experts in the welding sector are well conscious, understanding the causes, results, and avoidance techniques associated to porosity is essential for achieving durable and trustworthy welds. By delving into the origin causes of porosity, analyzing its detrimental results on weld top quality, and checking out effective avoidance strategies, welders can enhance their knowledge and abilities to produce top notch welds regularly.Usual Reasons of Porosity
Contamination, in the kind of dirt, oil, or rust on the welding surface, creates gas pockets when warmed, leading to porosity in the weld. Incorrect protecting occurs when the protecting gas, generally made use of in procedures like MIG and TIG welding, is incapable to totally secure the molten weld pool from reacting with the surrounding air, resulting in gas entrapment and succeeding porosity. Furthermore, insufficient gas insurance coverage, usually due to inaccurate circulation prices or nozzle positioning, can leave components of the weld vulnerable, allowing porosity to develop.Impacts on Weld High Quality
The presence of porosity in a weld can significantly compromise the overall quality and honesty of the bonded joint. Porosity within a weld creates voids or cavities that damage the framework, making it more at risk to splitting, corrosion, and mechanical failure. These spaces act as anxiety concentrators, lowering the load-bearing capability of the weld and enhancing the chance of early failing under used tension. Additionally, porosity can also function as potential websites for hydrogen entrapment, further exacerbating the destruction of the weld's mechanical properties.In addition, porosity can prevent the effectiveness of non-destructive screening (NDT) techniques, making it challenging to discover various other flaws or stoppages within the weld. This can result in considerable safety and security concerns, especially in essential applications where the structural honesty of the bonded parts is critical.

Prevention Techniques Introduction
Provided the detrimental effect of porosity on weld high quality, efficient avoidance methods are vital to maintaining the structural integrity of welded joints. Additionally, selecting the ideal welding criteria, such as voltage, existing, and travel rate, can help reduce the threat of porosity development. By incorporating these prevention methods right into welding techniques, the occurrence of porosity can be substantially linked here reduced, leading to stronger and extra reputable welded joints.Significance of Correct Protecting
Correct protecting in welding plays a critical role in preventing climatic contamination and making certain the stability of welded joints. Securing gases, such as argon, helium, or a combination of both, are typically utilized to secure the weld pool from reacting with components in the air like oxygen and nitrogen. When navigate to this website these reactive elements enter into call with the hot weld pool, they can trigger porosity, resulting in weak welds with minimized mechanical residential or commercial properties.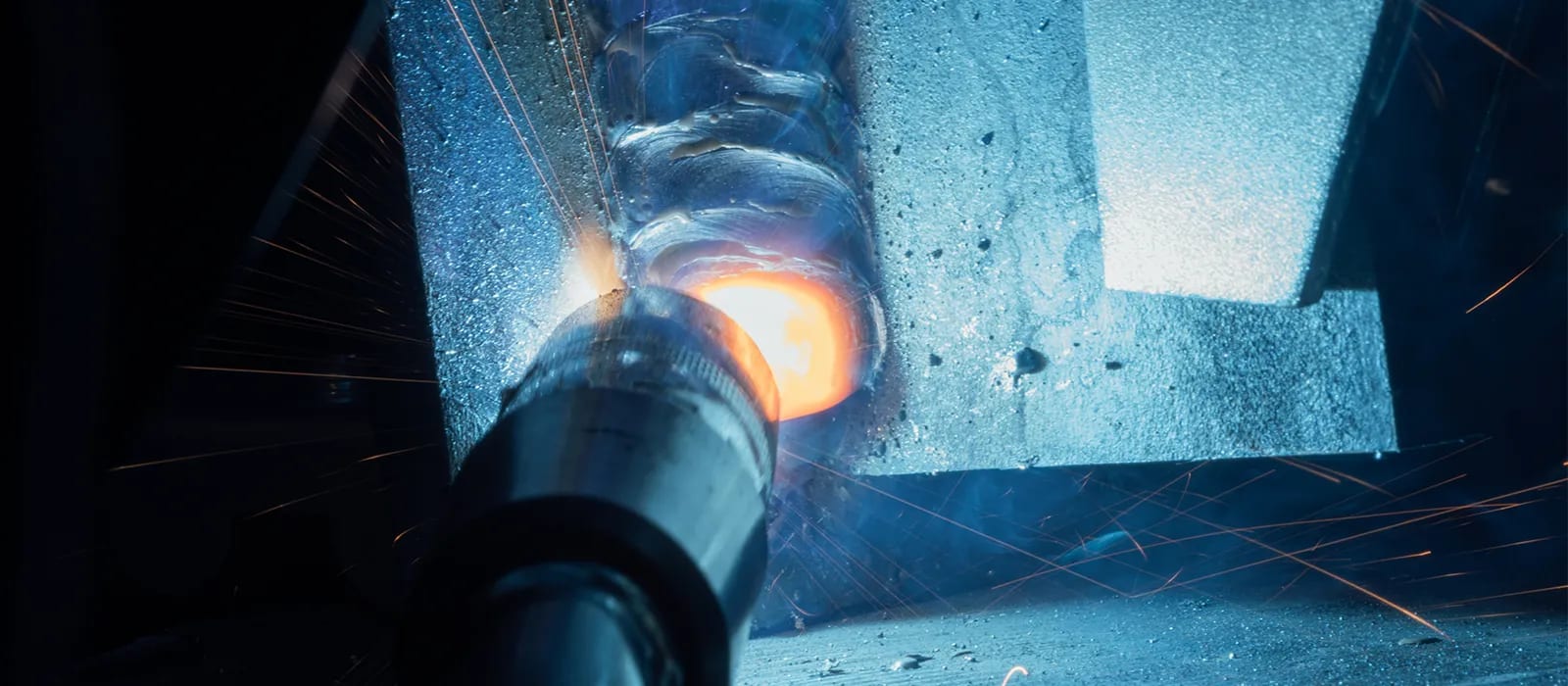
Poor securing can cause numerous flaws like porosity, spatter, and oxidation, jeopardizing the structural honesty of the welded joint. Consequently, sticking to proper protecting methods is vital to produce high-grade welds with marginal defects and make sure the long life and reliability of the welded elements (What is Porosity).
Monitoring and Control Methods
Just how can welders successfully keep track of and control the welding process to make sure optimal outcomes and prevent issues like porosity? One secret method is through using sophisticated surveillance innovations. These can include real-time tracking systems that give feedback on parameters such as voltage, present, take a trip rate, and gas flow prices. By continuously keeping track of these variables, welders can recognize discrepancies from the ideal problems and make instant adjustments to avoid porosity formation.
Furthermore, implementing correct training programs for welders is important for checking and controlling the welding process effectively. What is Porosity. Enlightening welders on the value of preserving regular parameters, such as correct gas shielding and take a trip rate, can help protect against porosity problems. Regular assessments and accreditations can also make certain that welders are proficient in tracking and controlling welding processes
Furthermore, the usage of automated welding systems can boost tracking and control capabilities. These systems can specifically regulate welding criteria, minimizing the possibility of human mistake and guaranteeing her response consistent weld top quality. By combining innovative surveillance innovations, training programs, and automated systems, welders can effectively check and control the welding procedure to reduce porosity issues and attain top notch welds.
Verdict
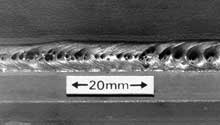
Report this wiki page